Tactile scans ... are worth the effort!
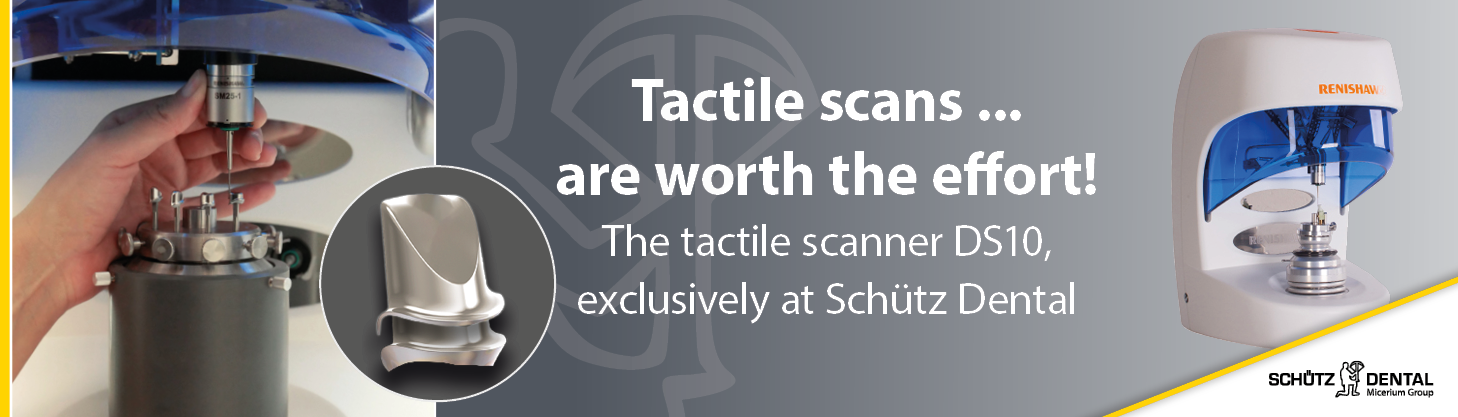
"Reproducible quality and fit - no matter, who operates the system."
The heart of the Complete Digital Workflow of Schütz Dental is, without a doubt, the tactile scanner. Schütz Dental recognized early on that such a scanner could revolutionize dental technology and negotiated exclusivity in the year 2014.
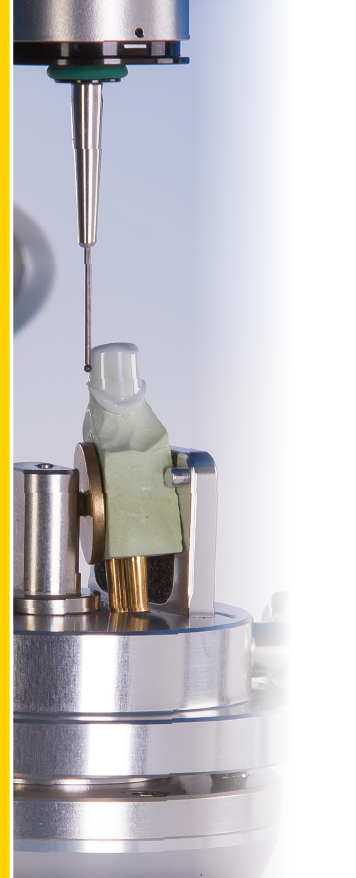
In 2014, Renishaw's dental scanner DS10 was introduced for the first time as a hybrid solution along with the optical scanner Tizian Smart Scan by Schütz Dental. While the jaw is scanned in an optical system, a single stump can be scanned with the highly precise tactile (= scan by touch) system by Renishaw. The data of both scans will be combined via CAD to a digital surface. The unique precision of the DS10 combined with an optical system is the secret to this dental scanner's success.
Heiko Müller, Managing Director of Renishaw GmbH: "The precision of DS10 was developed with help of our decade-long experience with the industrial coordinate measuring technique. The advantages cannot be ignored, especially for telescopic restorations, abutments and restorations with adhesive bases. Even in the ever-growing application area of implants and suprastructures, the Renishaw dental scanner avoids inaccuracies and stresses in advance because the DS10 accurately reproduces the position and alignment. We are pleased to have Schütz Dental as a reliable exclusive partner for sales and support at our side. This ensures that our customers receive fast and direct support and advice from a single source. This was an important fact in our decision making process pro Schütz Dental."
Today, about 10-12 % of German laboratories own a Renishaw DS10 or the predecessor model. Successful laboratories such as Claus Küchler Dental in Munich, Dentallabor Anger in Remagen and Wagner Zahntechnik in Ebsdorfergrund swear by the use of this tactile scanner.
Interview
Janine Wolf (Marketing Manager at Schütz Dental): Why did you decide on purchasing the tactile Scanner by Schütz Dental?
>> Claus Küchler (CKD): My life's work in dental technology is the double crown technique. I have been known in the industry for over 20 years as the inventor of the Telemaster. Back in 2014, I invested in scanning and modeling technology at Schütz. In 2018, the purchase of a tactile scanner from Schütz Dental followed out of conviction.
>> Michael Anger (Owner Anger Dentallabor, MA-CADCAM Service and dentalligent): At that time, I could already look back on a long and trusting relationship with Schütz Dental and knew that if this really worked the way my Schütz consultant described it to me at the time, it would be an absolute quantum leap for our industry. I've always been the type to try things out a lot and to keep looking for new ways to set myself up in the best possible way with my lab. A little over 10 years ago, I was therefore one of the first to use the Schütz tactile scanner. I still see on a daily basis that I had exactly the right instinct back then.
>> Vera Kittel (Lab Manager, Wagner Zahntechnik): Already 10 years ago, the combination technology was our spearhead. Then, as now, we were particularly well known for it. In 2017, we had our first good experiences with Schütz and the analog materials, which very quickly led to conversations about the digital workflow.
>> Christian Scholl (Managing Director, Wagner Zahntechnik): The advantages were simply convincing. That's exactly how we wanted to work, and today we can say that it was one of our best decisions to trust Schütz and focus on working with the tactile scanner.
Janine Wolf: How has the tactile scanner changed the way you work? How do you use it in everyday life?
>> Claus Küchler: In 2018, when the tactile scanner supported the first secondary design and the first milled secondary crown was on my table, I realized that the treads could not be produced by hand in this way. Since that moment, nothing has been cast in my lab. All work is milled. Currently, we produce 5 telescopic restorations per week. We mill at least one construction per night. In 80 % of the cases, the framework is milled right away, too.
>> Christian Scholl: The tactile scanner is in daily use at our company. It clearly revolutionized our combination work. Originally, we produced 4 combination restorations a week, but today we produce an average of 4 a day. Galvano technology is now history for us. Many work steps have been eliminated. As a result, we are much faster than we used to be, which makes it possible for us to do the high number of these actually very elaborate jobs - especially if they were to be produced in a completely analog way.
>> Michael Anger: It took about 3 to 4 years, but then we had made the complete switch from the conventional casting technique to working with the tactile scanner. At some point, one was no longer sufficient. Therefore, we have been working with two Renishaw DS10 scanners for some time now, both of which are in daily use. We produce telescopes, suprastructures, tertiary frameworks and everything that is on abutments with the tactile scanner. We produce 7-8 telescopes a day.
Janine Wolf: Michael, why did the complete switch take 3 to 4 years? Is that the time a newcomer should allow for the switch?
>> Michael Anger: Absolutely not! If the newcomer really wants to deal with this technology and the modern way of working, and gets help in the form of courses and exchanges with colleagues, it should take less than a year. As I said, I was one of the first back then and as one of the first, you can make the mistakes from which subsequent users benefit to a great extent. When I think about all the different materials and strategies we tried out back then, today it raises my hackles. But that was important and good, and it had to be that way, otherwise we wouldn't be where we are today. It's not for nothing that I spent years providing instruction on the scanner for the Schütz company and am still active in support today. And then, of course, you have to remember that times have changed. Many young colleagues want to work in this way and already have a basic understanding of technology and, above all, an interest in it. They are no longer interested in the conventional way of working, whereas back then it was of course a drastic change for established dental technicians.
Janine Wolf: What has the scanner done for you economically, but also for your reputation?
>> Claus Küchler: The economic improvement of the laboratory was noticeable directly after the introduction of digital technology and must be clearly emphasized. Immediately after the switch from one-piece casting to digital production, the results catapulted upwards. In fact, the active working time for a telescopic restoration is cut in half! The amount of telescopic restorations would be far from manageable if I had not switched to this technology 5 years ago.
>> Vera Kittel: As Christian said, we are much faster than before. We ourselves, our customers and, above all, the patients benefit from shorter procedures. Our dentist customers have always worked with us primarily because of our specialization in combination work. With the use of the tactile scanner, we were able to achieve a huge leap in quality. It has to be said that the amount of combination work we do would simply not be possible without the tactile scanner. What used to be done by 5 experienced steel technicians can now be done by 2 CAD/CAM technicians alone. Thanks to the Schütz tactile scanner, we were able to increase the number of our combination jobs fivefold.
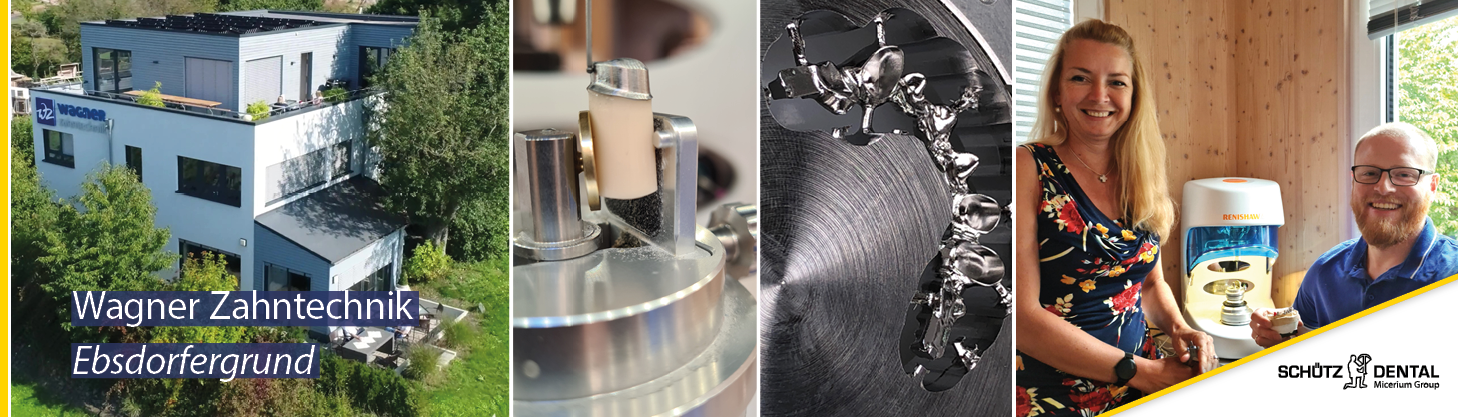
>> Michael Anger: With the entry into the digital world, every investment immediately had a positive impact. Currently, 5 of my employees, some of them from other professions, work for me on the orders that we realize with the tactile scanner - without the scanner, I would need 9 dental technicians for the same work. On the one hand, this is economical, and on the other hand, it is essential in view of the shortage of skilled workers. Thanks to the tactile scanner from Schütz Dental, my machine park has also grown quickly to ten machines. Let's think about that for a moment: The investment in a Tizian 3.5 Loader Pro+ is about as high as a good technician's annual salary, I need one technician to operate the machine, but without the machine I would need three technicians ... this should show everyone how sensible it is to invest in the Complete Digital Workflow. Of course, digitization, of which the Renishaw is a mainstay, has contributed to my good reputation and success, whether as a lab, milling or training center. But what I think is especially important to mention is that digitization has brought us dental technicians closer together. All of a sudden, there was an exchange between laboratories - maybe not necessarily with the direct neighbors, but nationwide, even internationally. This networking, which is so important and beautiful today, did not exist at all in the past. The technician sat as a loner in his laboratory over his work. This is a huge step forward and a benefit for our industry.
Janine Wolf: What are the clear advantages that make you not want to do without your tactile scanner anymore?
>> Vera Kittel: Our entire digital workflow is built on this system. We would not be able to maintain our productivity and schedule at all without it. The learning process is much shorter, the precision is extraordinary and the results are reproducible. No matter who operates it, it produces a perfect fit. That's totally great, a real process optimization. It would be an absolute step backwards for us into the 20th century if we had to do without this scanner - unthinkable.
>> Claus Küchler: If you want to produce real telescopes, controllable and reproducible, you can only do it with tactile scanning technology. A purely optical scan is not sufficient, as unpredictable results are produced. Only tactile scanning technology lets us work with parameters that are always the same. There is also a major advantage when considering framework production: modeling with a software facilitates the exact observance of layer thicknesses, which would not be possible with manual modeling. We produce highly stable, delicate constructions from non-precious metals that are robust and at the same time biocompatible. Base metal solders and casting shrinkage are a thing of the past. This technology also provides relief at the lab, with staff scanning and modeling, then reviewing and checking the work and preparing it for the night. All processes are production-safe and neatly timed. The repetition rate in production is not worth mentioning.
>> Michael Anger: Clearly the predictable and reproducible results! I need this consistently accurate technology and certainty about the result I get the next day. Second clear advantage: The tactile scanner works without scan spray and is therefore simply unbeatable in terms of precision, because without a doubt any spray adds size and forms puddles. Even if this should be minimal, it is still there. And yes, of course, we used to get along without tactile scanning technology, but then it was not uncommon to have to tackle a job several times. The "human" factor is a weak point in this case. By using these high-precision conescopes, I get flawless results: no more wedging or jamming, no more cold welding, and most importantly, no more fitting work by dentists and dental technicians inside the patient's mouth. I don't have to go to a dental office to loosen up a restoration because the patient can't get it out after it has been inside the mouth for 3 days and it has become quite unpleasant.
Janine Wolf: Why is Schütz Dental one of your most important partners?
>>Christian Scholl: So far, we have only talked about the tactile Scanner. In our opinion, however, the all-encompassing range and the interaction of the systems we get at Schütz is the ne plus ultra. The tactile scanner in conjunction with our Tizian Cut 5.2 machines (now the Tizian 3.5 series), the CAD and CAM control, etc. is only what actually makes it so ingenious and exciting. Yes, of course you can scan with the tactile scanner yourself and then send the data to a milling center, but this is not our way. For us, the effectiveness comes primarily from the fact that we use these high-quality data to mill the restorations ourselves with the machines of our choice, the perfectly coordinated milling strategies and, of course, the right materials. We get all this and more directly from a single source at Schütz. We know that with Schütz we have an absolutely reliable partner. We greatly appreciate the network, the training offers, the service and support, of which I am now allowed to be a part myself. In total, more than 35 external specialists work with and for Schütz Dental; in this circle, there is a suitable answer to every question or every task.
>> Vera Kittel: You really get that much support, which I can only recommend to newcomers in particular, but also to experienced colleagues. Schütz does not leave you alone after the delivery of the systems, but accompanies the laboratories into the work process, so that you can integrate the new systems and workflows into your individual business very quickly and very successfully. I believe that you really only get this at Schütz and nowhere else.
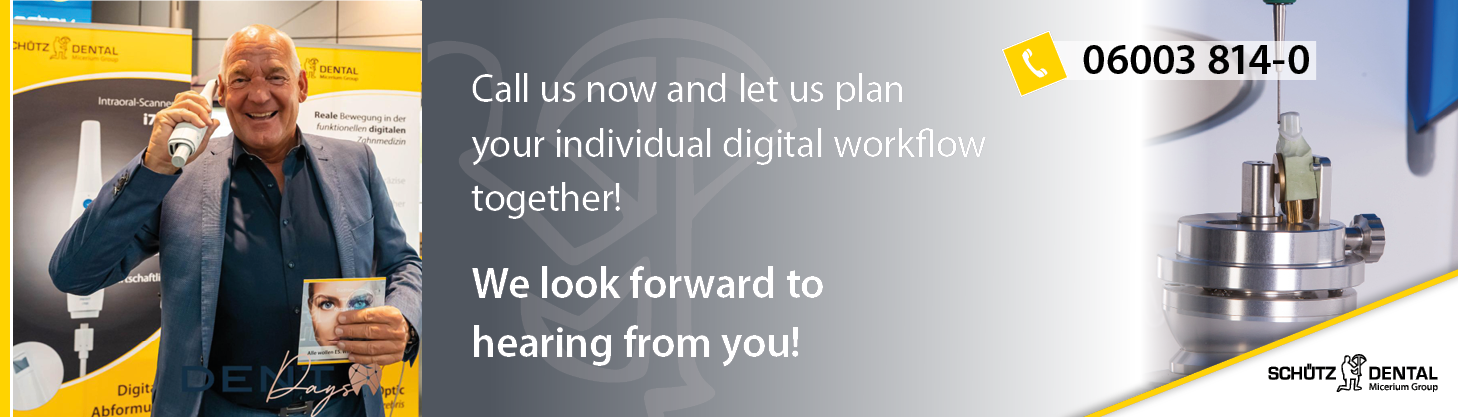
Illustrations may vary. Product, technical data and prices are subject to change without notice.